Just how to Recognize What is Porosity in Welding and Improve Your Strategy
Just how to Recognize What is Porosity in Welding and Improve Your Strategy
Blog Article
The Scientific Research Behind Porosity: A Comprehensive Overview for Welders and Fabricators
Recognizing the complex systems behind porosity in welding is critical for welders and fabricators aiming for impeccable craftsmanship. As metalworkers dig into the midsts of this sensation, they discover a globe governed by various factors that influence the development of these minuscule voids within welds. From the make-up of the base products to the ins and outs of the welding procedure itself, a wide variety of variables conspire to either worsen or minimize the presence of porosity. In this comprehensive guide, we will untangle the science behind porosity, discovering its results on weld high quality and introduction advanced strategies for its control. Join us on this journey via the microcosm of welding imperfections, where accuracy meets understanding in the quest of remarkable welds.
Comprehending Porosity in Welding
FIRST SENTENCE:
Assessment of porosity in welding discloses crucial understandings into the integrity and high quality of the weld joint. Porosity, defined by the visibility of tooth cavities or spaces within the weld metal, is a common problem in welding processes. These voids, otherwise correctly resolved, can jeopardize the structural stability and mechanical homes of the weld, bring about possible failings in the ended up product.

To spot and evaluate porosity, non-destructive testing approaches such as ultrasonic screening or X-ray inspection are often used. These techniques permit the recognition of internal defects without jeopardizing the integrity of the weld. By examining the dimension, form, and distribution of porosity within a weld, welders can make educated decisions to boost their welding processes and accomplish sounder weld joints.

Aspects Influencing Porosity Development
The incident of porosity in welding is affected by a myriad of variables, ranging from gas shielding performance to the complexities of welding criterion setups. Welding parameters, consisting of voltage, present, travel speed, and electrode type, additionally effect porosity formation. The welding technique employed, such helpful hints as gas steel arc welding (GMAW) or secured metal arc welding (SMAW), can influence porosity development due to variants in warmth circulation and gas coverage - What is Porosity.
Effects of Porosity on Weld High Quality
The presence of porosity also deteriorates the weld's resistance to rust, as the trapped air or gases within the voids can respond with the surrounding atmosphere, leading to deterioration over time. Additionally, porosity can prevent the weld's capability to endure stress or impact, further threatening the overall high quality and reliability of the welded structure. In critical applications such as aerospace, automobile, or architectural buildings, where safety and toughness are critical, the destructive effects of porosity her latest blog on weld top quality can have severe effects, highlighting the value of decreasing go to website porosity through appropriate welding techniques and treatments.
Techniques to Reduce Porosity
Additionally, utilizing the proper welding criteria, such as the right voltage, existing, and travel speed, is essential in preventing porosity. Keeping a regular arc size and angle throughout welding likewise assists decrease the likelihood of porosity.

Utilizing the appropriate welding method, such as back-stepping or utilizing a weaving movement, can also aid distribute heat uniformly and reduce the possibilities of porosity formation. By implementing these strategies, welders can efficiently lessen porosity and generate premium welded joints.
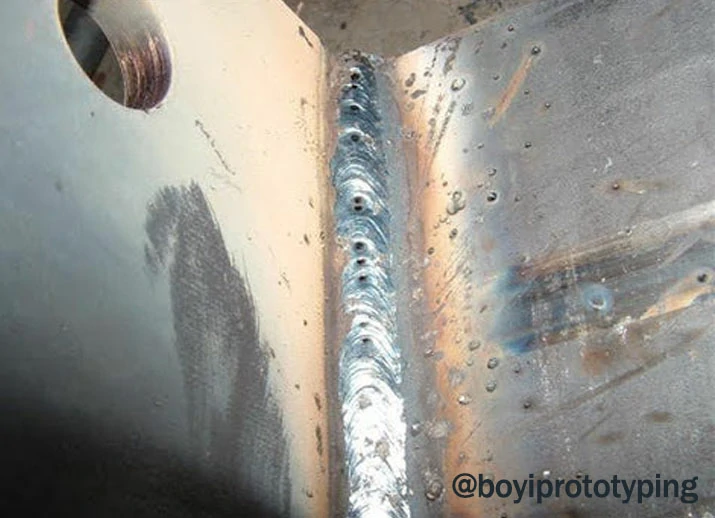
Advanced Solutions for Porosity Control
Executing sophisticated technologies and ingenious techniques plays a crucial function in accomplishing superior control over porosity in welding processes. One sophisticated solution is using sophisticated gas mixtures. Shielding gases like helium or a blend of argon and hydrogen can help in reducing porosity by giving much better arc security and enhanced gas insurance coverage. Additionally, using advanced welding methods such as pulsed MIG welding or changed atmosphere welding can likewise aid reduce porosity concerns.
One more sophisticated remedy entails the use of advanced welding devices. Using devices with built-in attributes like waveform control and innovative power resources can boost weld quality and decrease porosity risks. The implementation of automated welding systems with exact control over specifications can substantially reduce porosity defects.
Furthermore, incorporating innovative surveillance and examination modern technologies such as real-time X-ray imaging or automated ultrasonic screening can aid in detecting porosity early in the welding procedure, allowing for immediate rehabilitative activities. Generally, integrating these advanced services can significantly improve porosity control and improve the overall high quality of welded parts.
Final Thought
In conclusion, recognizing the science behind porosity in welding is essential for welders and makers to create premium welds. By identifying the variables affecting porosity development and implementing methods to reduce it, welders can boost the overall weld top quality. Advanced solutions for porosity control can further improve the welding procedure and make sure a strong and trusted weld. It is very important for welders to constantly inform themselves on porosity and carry out ideal methods to accomplish optimum results.
Report this page